When every minute counts – How we helped Getinge double their production capacity
Getinge is a global medical technology company that provides hospitals and life science institutions with products and solutions that aim to improve clinical results and optimize workflows. The offering includes products and solutions for intensive care, cardiovascular procedures, operating rooms, sterile reprocessing and life science. During Covid-19, the company is helping caregivers to save lives through the manufacturing and distribution of ventilators and oxygenators. Getinge has more than 10,000 employees worldwide and is a market leader supplier of intensive care ventilators, which puts the company in a unique situation due to the Covid-19 pandemic.
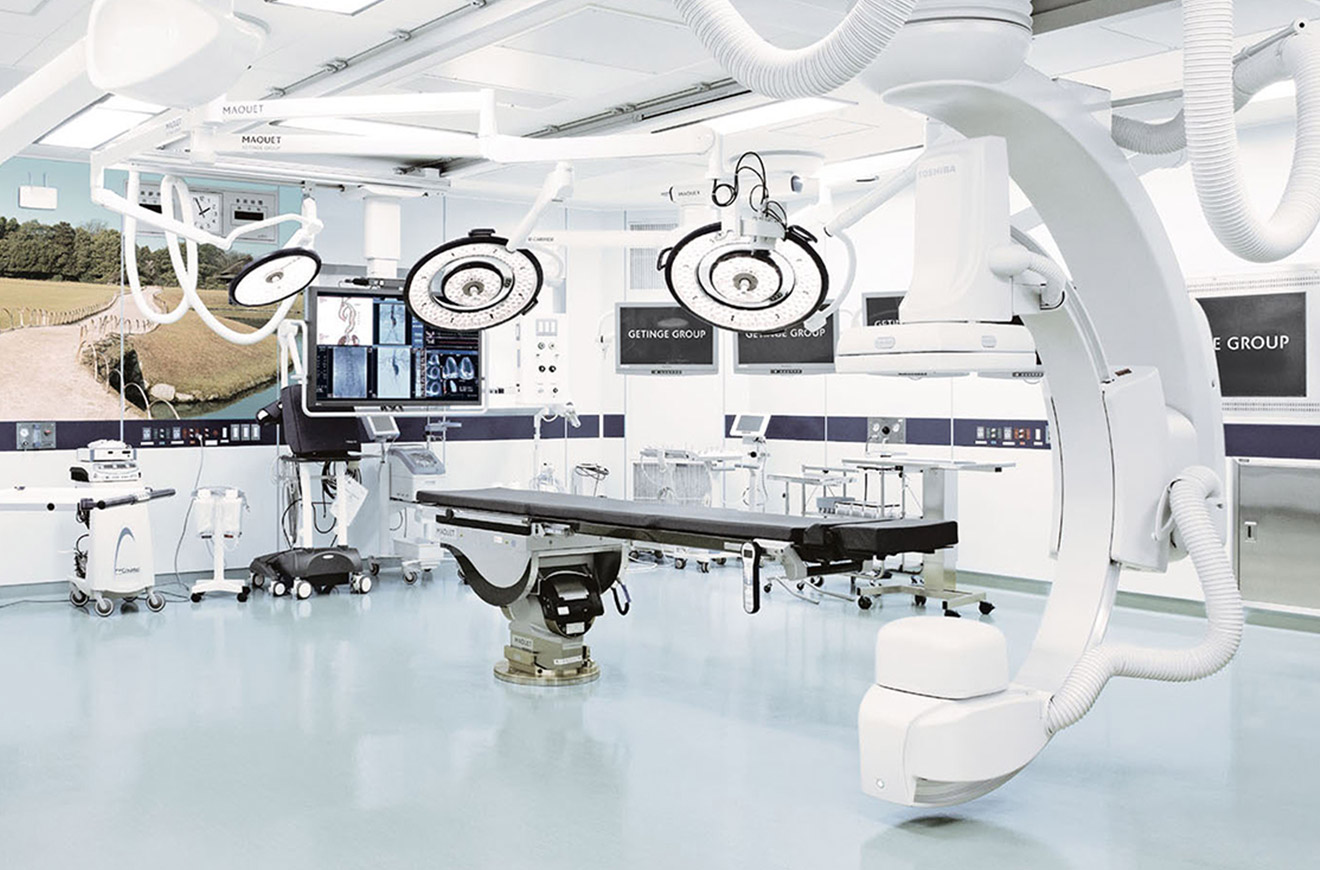
Throughout the spring, the demand for ventilators has exploded and Getinge has had to double production in less than a couple of weeks. This means unprecedented pressure on management and planning. By engaging in, a so-called ramp-up, Getinge has been able to systematically match the sudden need for advanced ventilators for Intensive Care Units worldwide. The main challenge, however, has been the subsequent ramp-up for supply. ‘It is crucial for us at this moment that our global supply chain of components and parts can correspond to our volumes,’ said Mattias Perjos, President & CEO at Getinge in an interview with Swedish weekly newspaper Affärsvärlden in March.
During the first week of April, Getinge was well underway by temporarily hiring staff from Scania, cleverly employing furloughed engineers and operators. With a planned production increase of 160 per cent compared to 2019, workers were needed for the assembly line in Solna, Sweden. And it did not take long before the halls were filled with people, keen to start helping to increase the production of ventilators. However, to secure the assembly, supply needed to match the added shifts that were now put in place.
The task at hand, quickly became to track deliveries of the components carefully, increasing visibility into every physical transport, an assignment given to Sonat. In normal circumstances, delivery is monitored but not controlled, since most assembly lines have a small stock and can continue production, even with minor delivery delays. With the dramatic demand for ventilators from emergency rooms across the globe, margins of error had to be eliminated. A delay in the delivery of components, during the ramp-up, would instantly cause a standstill and jeopardise the ability to serve needing patients across the globe. ‘At Sonat, we have both knowledge and experience from former ramp-ups, and we are used to working under this sort of pressure. We track the supply chain manually and utilise our network to secure location data and progress. Once we know more, it is easy for us to re-align and make each delivery more effective. We start informing the planning team on the first day of commission,’ says Kjell Rundqvist, Account Manager for Getinge at Sonat.
Quicker supply chain visibility is one of the most prominent skills that Sonat has developed at Getinge for the success of the ramp-up. While many companies of Getinge’s volume have great insight into production, there are large gaps in the tracking of in-flow. ‘We begin by asking a new set of questions. And we manually track individual orders via telephone and mail, which quickly gives us control over critical incoming deliveries’, says Rundqvist.
At noon, daily, the Vice President for Getinge’s Solna factory meets up with her program managers, account managers and production managers to get an update on manufacturing and distribution. The room is full of people, facing six large screens with data, the pressure is high to make the right production decisions based on the resources given. Sonat is part of the briefing, leaving fresh reports of the latest movements, a tracking Getinge previously lacked, but a vital step in the process of getting the ventilators to those who need them fast.
’Not having enough knowledge of daily deliveries made everything unmanageable. The sporadic tracking we can live with during normal circumstances is not enough with people waiting inside production, ready to assemble. Instead, we need full visibility into every order,’ says Nina Wenell, Supply Chain Manager at Getinge.
Through skills that Sonat has been able to develop at Getinge, the company is now nimble enough to scale quickly with need. From now on, the increased production and larger supply volume will become a norm, and instant visibility will become less critical. And Rundqvist admits, it is in the ramp-up the visibility becomes a crucial success factor. ‘The way in which Sonat has enabled insights at Getinge is related to agility and crisis management. As an alliance we will reach greater outcomes and save even more lives.’